May 23, 2025
Rust and corrosion silently threaten heavy-duty trucks, especially in coastal or high-salt areas. Prioritize regular underbody washes, rust-inhibitor sprays, and early surface rust repairs. Protect key systems like brake lines, frames, and battery grounds with targeted maintenance and corrosion-resistant materials to ensure safety, reliability, and longer fleet life.
.webp)
Understanding Rust and Corrosion
Between unpredictable weather patterns, exposure to road salts, and humid winds, the conditions for rust and corrosion are ever-present. When metal is exposed to moisture and oxygen, oxidation occurs—rust forms. Left unchecked, it deteriorates not just aesthetics but also critical systems like:
- Brake lines
- Fuel tanks
- Frames
- Electrical grounding
Corrosion isn’t just surface deep; it compromises structural integrity, leading to unexpected repairs and even safety hazards. For fleet operators and owner-operators alike, preventing rust and corrosion in heavy-duty trucks is not optional—it’s essential.
High-Risk Components and Systems
Frames and Chassis
Truck frames and chassis are the skeletons of your rig. Unfortunately, they’re also a hot zone for corrosion. The undercarriage gets sprayed with road salts, grime, and water—especially during coastal runs or winter operations in Texas.
Brake and Fuel Lines
Made from steel or aluminum alloys, brake and fuel lines are prone to pitting and weakening over time. Corrosion here isn’t just a nuisance—it’s a liability.
Battery Terminals and Electrical Grounds
Electrical systems rely on clean, solid grounding. Corroded battery terminals and grounds cause voltage drops, poor sensor readings, and ECM faults.
Proactive Strategies to Prevent Corrosion
Regular Steam Cleaning and Underbody Washes
Routine cleaning is your first line of defense. Use a high-pressure washer or steam cleaner to remove road salts, dirt, and debris from the undercarriage and wheel wells. Pay special attention to:
- Leaf spring hangers
- Air tanks and lines
- Mud flaps and splash zones
In coastal and high-humidity regions like Austin and San Antonio, increase the frequency of these cleanings—at minimum, monthly.
Rust-Inhibitor Sprays and Undercoatings
Apply professional-grade rust inhibitors, especially after every deep clean. Products like wax-based sprays or oil-based coatings can seal metal from moisture and air. Popular choices in the industry include:
- Lanolin-based sprays
- Petroleum-based undercoatings
- Zinc-rich primers for high-touch repairs
Make it part of your preventive maintenance routine, particularly during pre-winter prep or when seasonal road treatments begin.
Addressing Surface Rust Early
Surface rust is the early warning sign. If caught in time, it’s reversible. Here’s what to do:
- Sand or wire-brush affected areas until clean metal is visible.
- Apply a rust converter, which chemically neutralizes iron oxide.
- Follow with a primer and high-quality enamel paint.
Touch-ups may not seem glamorous, but they extend the service life of your truck significantly.
Component-Specific Tips for Corrosion Control
Brake and Fuel Line Protection
Install protective sleeves on brake lines or switch to stainless steel when replacing components. Also:
- Use dielectric grease at sensor connectors.
- Periodically inspect junction points and clamps.
Battery Terminals and Grounds
Apply high-quality corrosion inhibitors to battery terminals to prevent oxidation. Ensure all connections are tight, clean, and free from rust or acid buildup. During scheduled preventive maintenance, technicians should conduct a voltage drop test across major grounding points to identify any resistance caused by corrosion.
Wheel Hubs and Bearings
Grease seals are the first defense against moisture intrusion and bearing failure, but they’re only effective if intact and properly seated. Check for cracking, splitting, or displacement of seals during wheel-end inspections.
Seasonal Considerations
Through snow and ice, trucks face calcium chloride and magnesium chloride sprays. Upon return:
- Perform a full undercarriage inspection
- Reapply undercoating as needed
- Clean with neutralizing agents that remove chemical residues
Salt deposits left untreated lead to galvanic corrosion, especially where dissimilar metals meet—like aluminum cabs and steel frames.
Incorporating Corrosion Control into Your PM Schedule
Incorporating corrosion mitigation into your PM intervals ensures consistency. Consider:
- Quarterly inspections for surface corrosion
- Bi-annual reapplication of undercoatings
- Annual frame rustproofing touch-ups
Technicians can integrate these checks into existing workflows, such as DOT compliance reviews.
Investing in Corrosion-Resistant Components
More fleets are shifting toward stainless steel hardware, aluminum toolboxes, and composite body panels. These materials offer long-term protection against environmental wear and tear.
- Stainless U-bolts and brackets reduce rust streaking.
- Aluminum fuel tanks resist salt spray better than steel.
- Nylon air lines don’t corrode like copper or steel.
Protect Your Fleet From Rust
Preventing rust and corrosion in heavy-duty trucks is an investment in safety, performance, and fleet longevity. From routine cleanings and undercoatings to choosing corrosion-resistant materials, proactive care goes a long way. Don't let rust be the silent killer of your trucks. Prioritize protection and stay ahead of the wear.
AFS News & Articles
Read About The Latest in Industry
Here, you'll find regular articles covering a wide range of topics related to diesel repair, maintenance, and troubleshooting. Whether you're an operator, fleet manager, or diesel engine enthusiast, you'll find something of interest here.
.jpg)
How to Improve the Longevity of Your Truck’s Transmission
Extend your truck’s transmission life with proper fluid care, heat management, preventive maintenance, and smart driving habits. Learn essential tips to avoid costly breakdowns and keep your fleet running reliably in Texas.
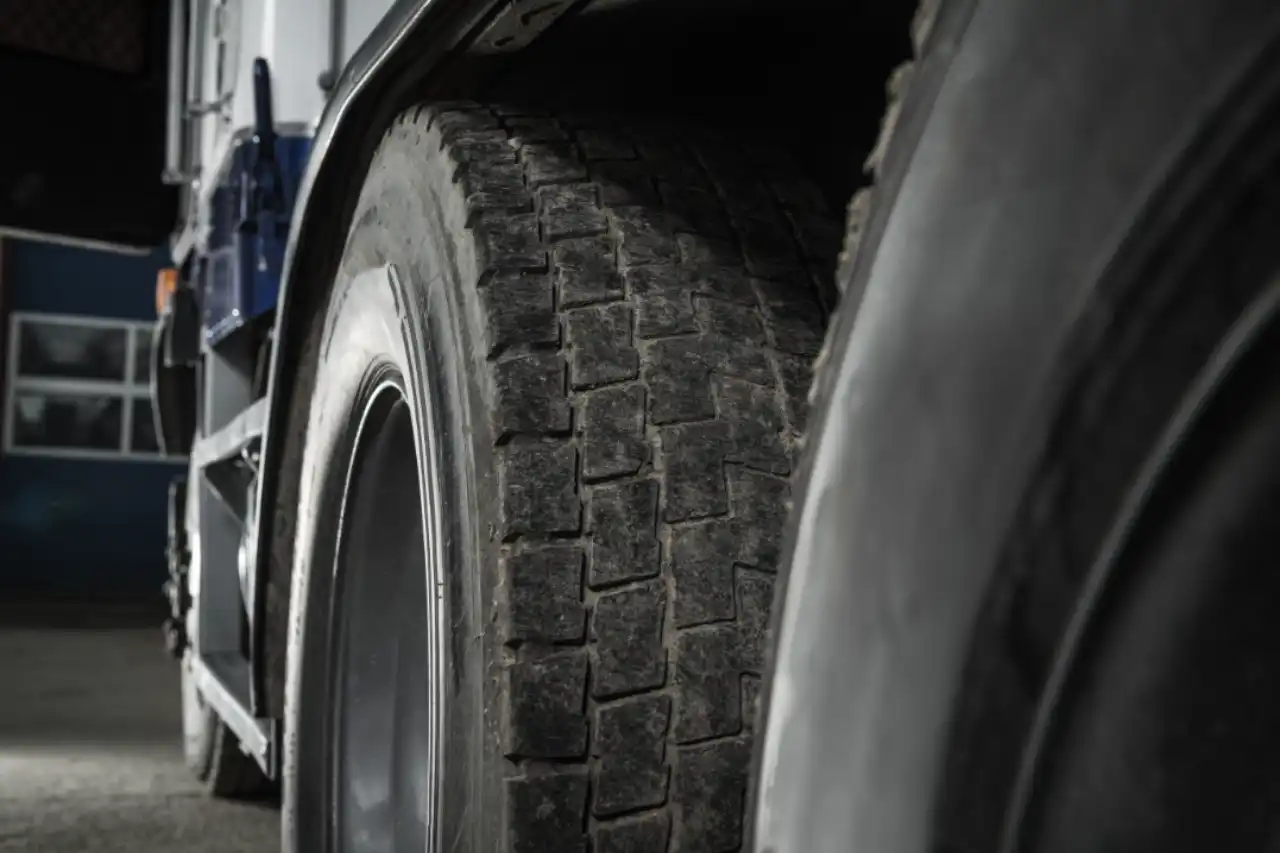
The Importance of Regular Truck Tire Inspections
Regular truck tire inspections improve fuel efficiency, prevent costly blowouts, ensure DOT compliance, and extend tire lifespan. Stay proactive to keep your fleet running safely.
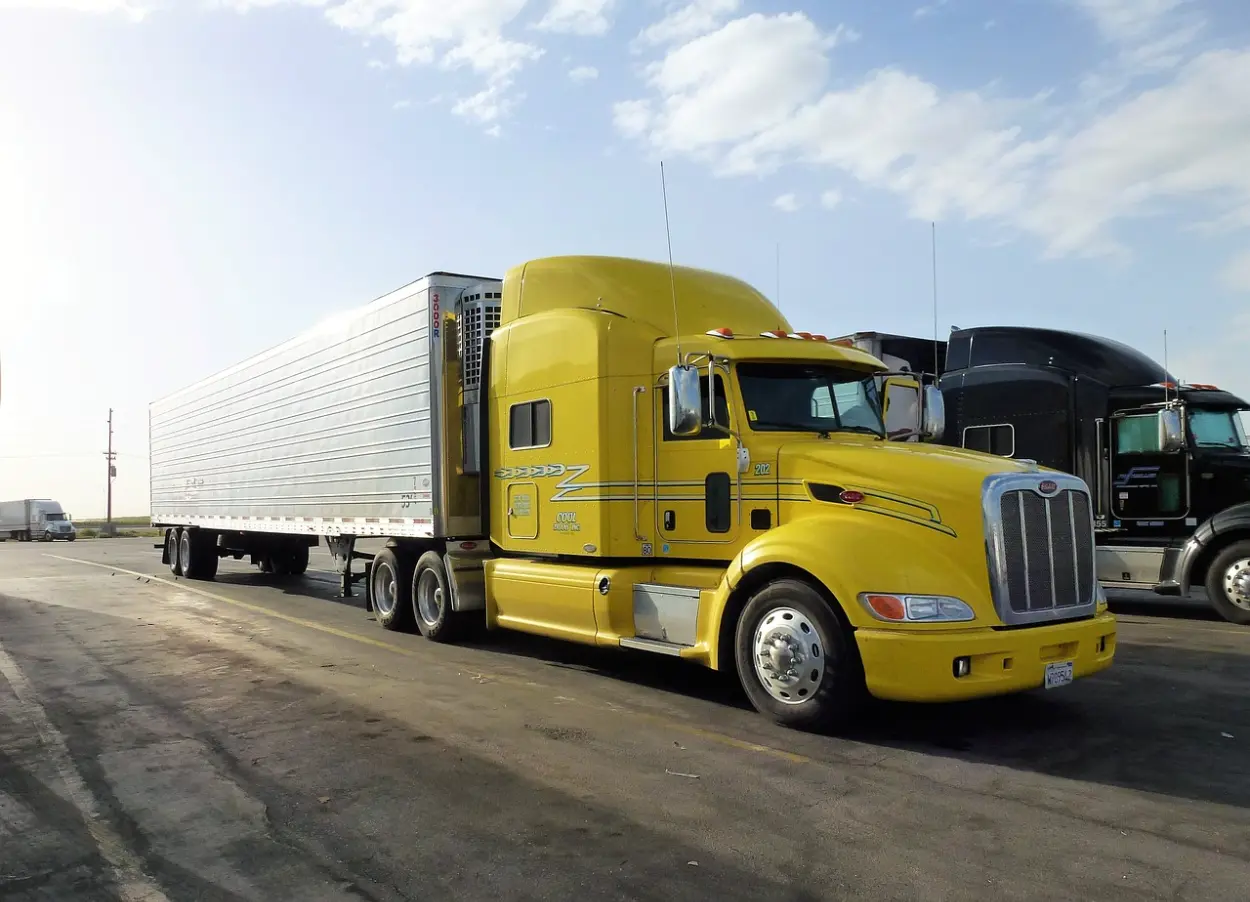
When to Replace Your Truck’s Air Filters: Key Signs
Replace your truck's air filter when you notice reduced fuel efficiency, loss of engine power, black exhaust smoke, unusual noises, or visible dirt. Regular checks every 10,000-15,000 miles and using quality filters help maintain engine performance, reduce emissions, and prevent costly repairs.
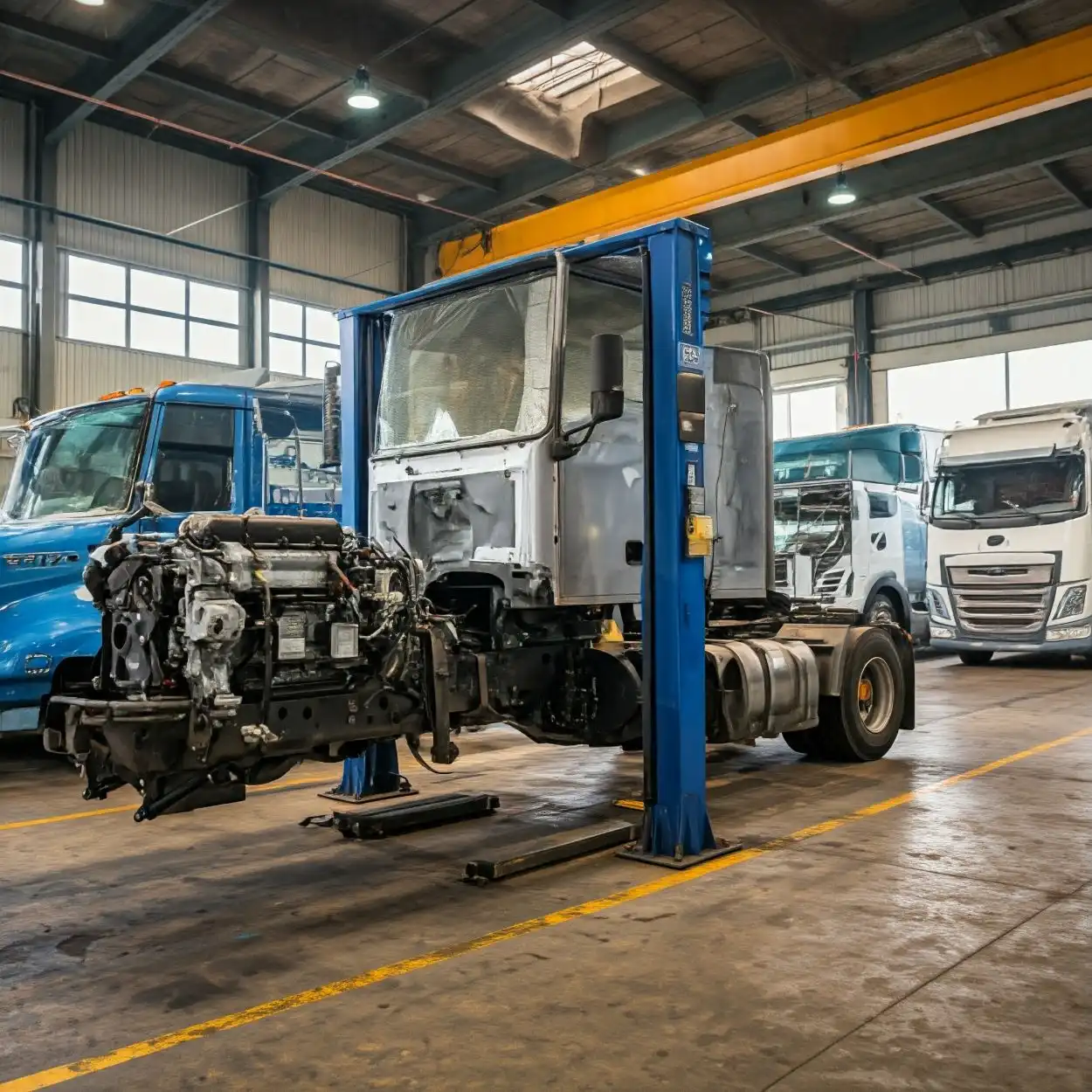
Top 5 Common Diesel Engine Problems and Their Solutions
Learn about the top 5 common diesel engine problems like hard starts, black smoke, and overheating, and their solutions for drivers in Austin and San Antonio, TX.
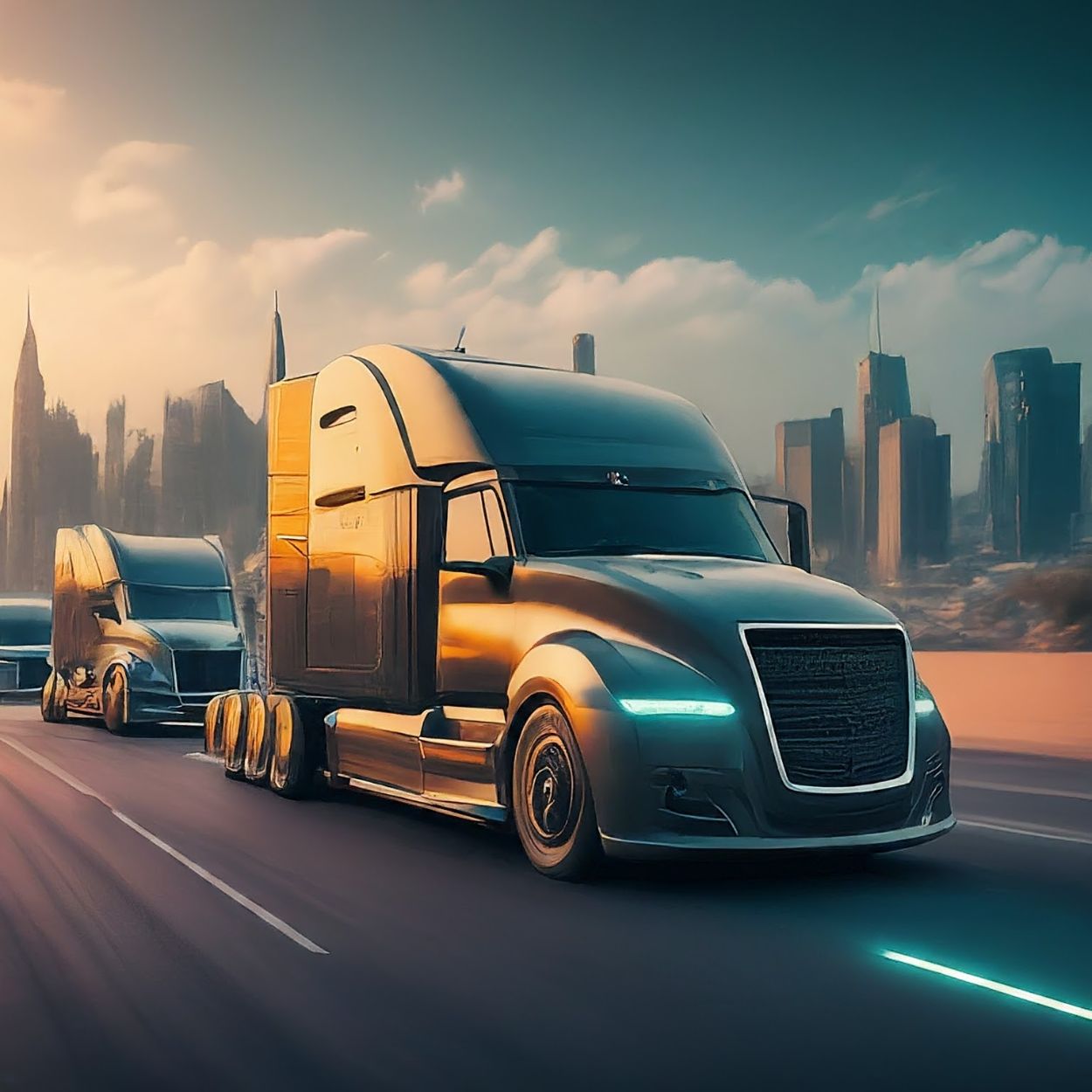
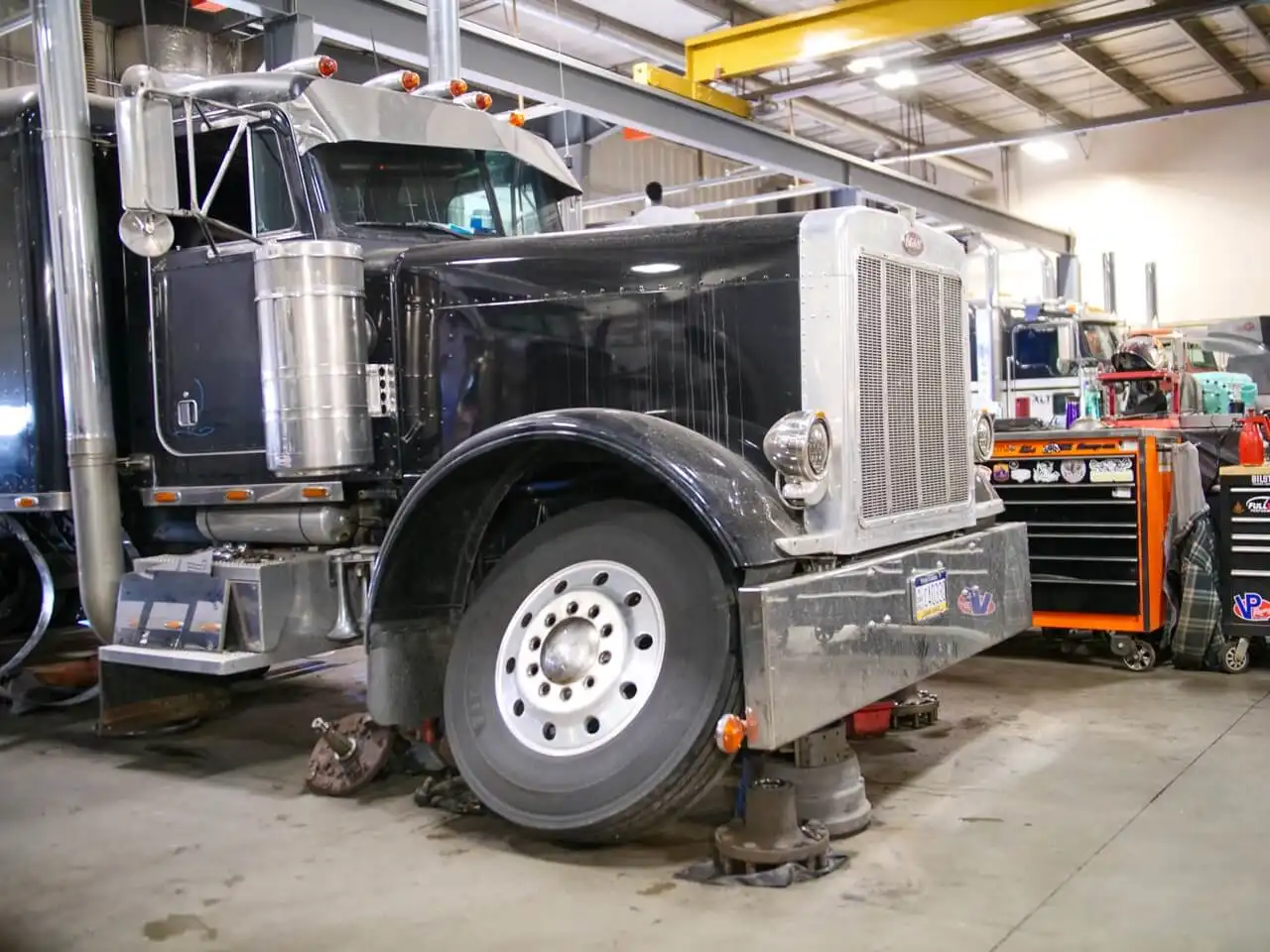
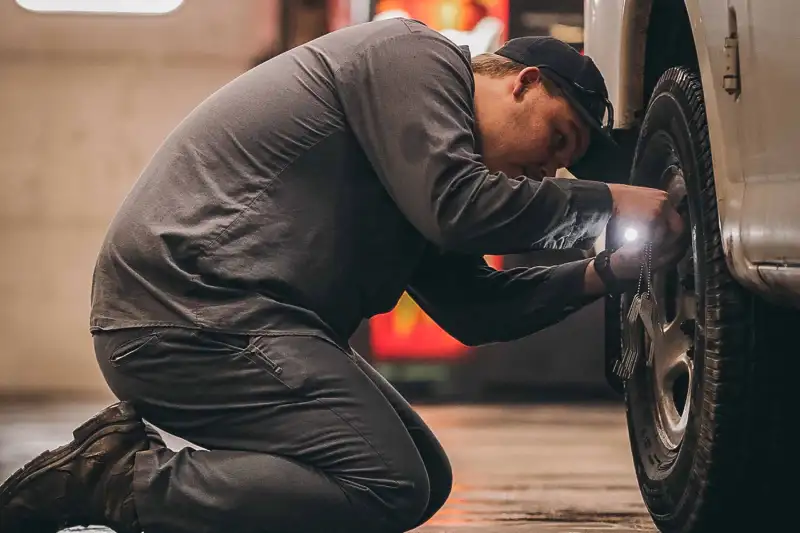
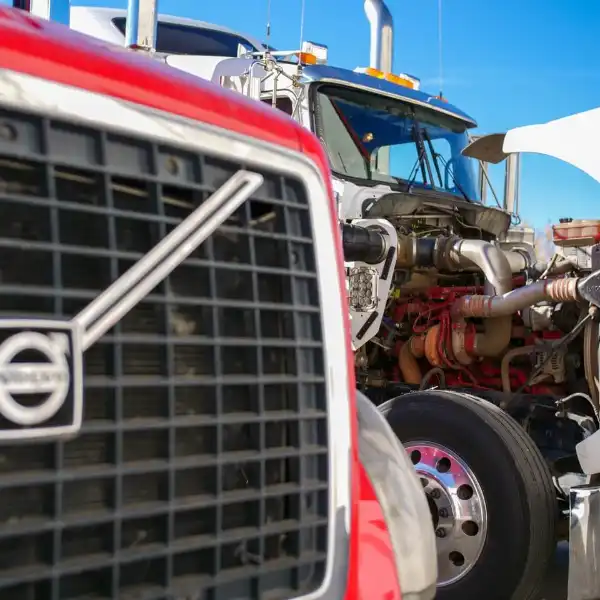
4 Diagnostic Tips and Tricks to Overcome EGR & DPF Issues
Beat downtime & repair costs! Learn how to diagnose & fix EGR & DPF problems in your commercial trucks. Includes cleaning methods, preventative tips & more.
.webp)
The Latest Advancements & Benefits of Diesel Technology
Diesel engines are an essential part of our daily lives, powering everything from cars and trucks to trains and boats.
Why Choose AFS Truck & Auto Repair Center?
We can come to you!
Our Patented Service Vehicles are specially designed and equipped to perform 85% of all vehicle maintenance and repair requirements on site.
"William is a awesome guy. He did a great job. Called about the tandem axle not sliding and helps me fixed some other little issue. I definitely recommend austin fleet services"
"These guys are great, had an emergency with a DEF pump on a black Friday, only shop that picked up the phone, took my driver in immediately and didn't give me the runaround like most do now. I asked not to diagnose anything and just change the pump. Truck back on the road in 3-4 hours and saved us at least 3 days waiting for another shop to open. Definitely coming back here next time our trucks are in the area!"
"Outstanding experience with AFS and George, their knowledgeable mechanic who replaced my valve cover gasket. My vehicle is running smoother than ever. Thank you AFS!"
Contact Us
Get in touch with AFS Truck & Auto Repair Center today to schedule service in-shop in San Antonio or Austin & Pflugerville, or via mobile service in the surrounding areas.
Pflugerville, TX 78660
San Antonio, TX 78219